How to Measure a Propeller or Impeller Diameter
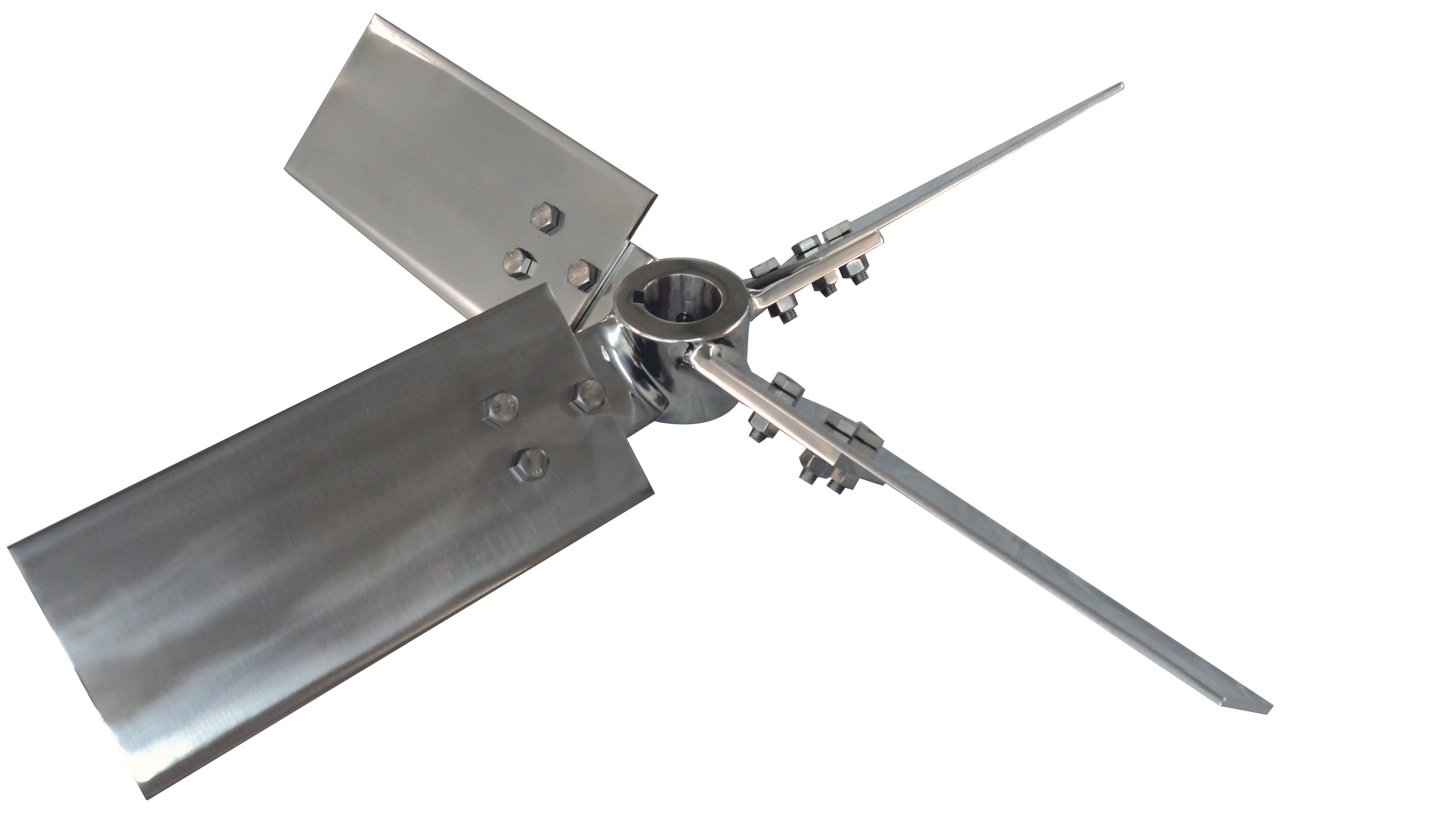
When it comes to ensuring that the process outcome from utilizing an industrial mixer to produce liquid products is a success, the mixing impeller plays a critical role. After all, it’s the mixing impeller that is in direct contact with the batch contents and dictates the flow volume and agitation intensity. This is true whether the impeller design is a common marine style propeller or one of many other popular styles, including hydrofoils and pitched blade turbines, also referred to as axial flow turbines . As basic as it sounds, there is one characteristic of the mixing impeller that requires an accurate determination – its diameter.
What Is Impeller Diameter?
The impeller diameter is the distance across the circle that a rotating impeller creates when measured directly through its center. The diameter of a circle is the distance from any point on the circle straight across the center to the opposite side of the circle.
As a general guideline for lower viscosity liquids a good starting point for impeller diameter is one-third the diameter of the mixing tank. Example: If your mixing tank has a diameter of 18 inches, a 6” diameter impeller is a good choice for most liquids. This is known as the impeller diameter to tank diameter (D/T) ratio. Variation from this reference point can be driven by material properties of the mixed liquid; higher viscosities can demand a larger D/T ratio and lower viscosities can be agitated with smaller impellers rotating at a higher rotational speed.
Accurate measurement or selection of the mixing impeller diameter, in addition to selection of its design, is key to a mixing system as it dictates the flow pattern within the mixing tank or vessel.
Measuring the Diameter of an Impeller
In measuring impeller diameters of designs that feature even-numbered blades, like a 2-bladed or 4-bladed impeller, simply measure the point from the outermost tip of the blade across the center of the impeller bore, or center hole, to the outermost tip of the opposite blade.
The confusion lies when measuring impellers with an odd number of blades, like a 3-bladed impeller. In measuring a 3-bladed propeller or impeller, you do not have a blade exactly opposite across the hub’s bore. The trick is to measure the radius and multiply it by 2 to get the diameter. Measure the distance from the outermost tip of the blade to the center of the bore to obtain the radius. This provides the impeller radius, which is then doubled to determine the diameter.
For example, a mixing impeller that measures a radius of 3” from the tip of the blade to the center of the bore will have a diameter of 6”. (A 3” radius multiplied x 2 equals a 6” diameter.)
Factors to Consider Around Mixing Propeller or Impeller Diameters
Accurately measuring or choosing a mixing propeller or impeller diameter is very important when replacing impellers on an existing mixer or when specifying one for use in a new application.
Power
Due to the exponential role diameter plays in power consumption, it needs to be understood that upsizing the impeller size on a mixer warrants evaluation to prevent thermal motor failure that comes from being overloaded.
Torque Evaluation
Even for systems that feature a gearbox to reduce motor speed, the change in required torque should be assessed when impeller size is increased, especially if the increase is significant. When sourcing replacement impellers, measuring the original components as accurately and precisely as possible is important.
Durability Issues
Blade wear or damage should be taken into account to ensure the replacement is as close to the original as possible. Consulting INDCO’s standard impeller size tables is a great place to start. However, if the original impeller is between sizes or otherwise non-standard, consult with customer service as we can match custom requirements when specified
Selecting the Proper Impeller Size and Motor for Your Mixing System
The Right Consultation for the Right Impeller Size Selection