How to Extend the Lifespan of Your Heavy Duty Mixer
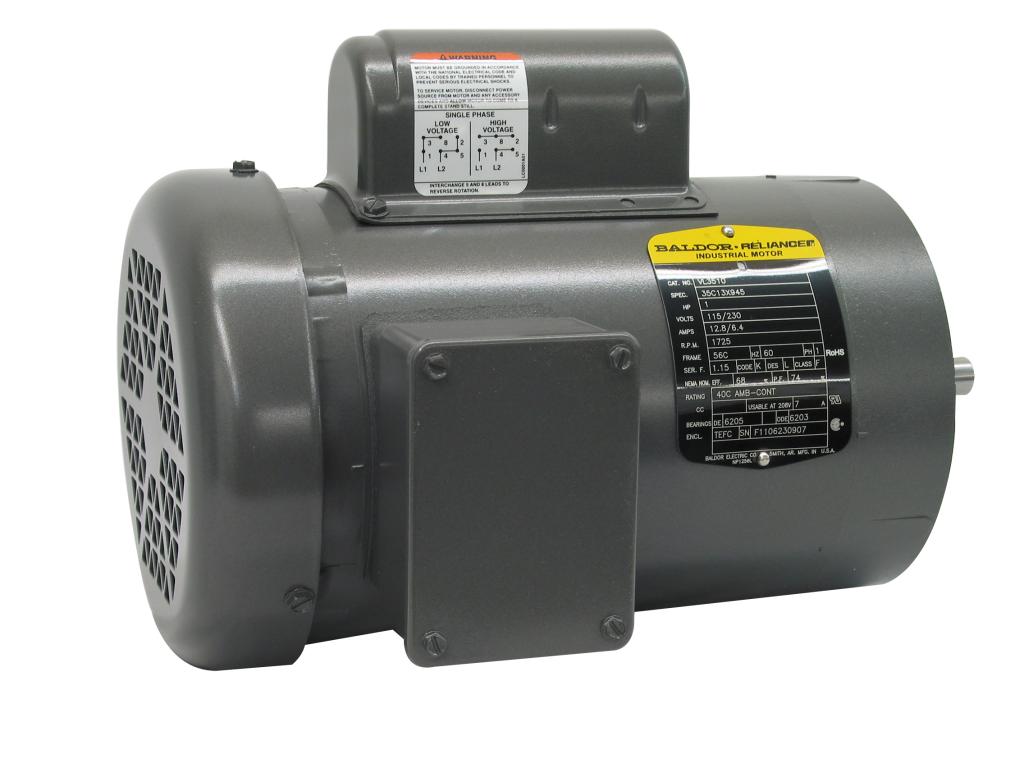
It’s no secret that within the industries who utilize heavy duty mixers the star player is the mixer itself. This essential piece of equipment is counted on day in and day out and year after year to produce consistent output at the highest level—hopefully without the machinery wearing out or needing multiple, costly repairs. On average, a heavy duty mixer can last anywhere from 10-20 years and may even go beyond that if the proper measures are taken to ensure its health and functionality.
To avoid any problems and get the best return on your investment, it’s vital that routine maintenance and care be applied to your commercial mixer machine so that it can go the distance.
How can you extend the lifespan of your heavy duty mixer and help your workflow be more efficient? Continue reading below for a few of INDCO’s top tips.
Adopt a Routine Cleaning and Maintenance Schedule
To ensure the longevity of your mixing equipment, maintenance is key. Your industrial mixer should be thoroughly cleaned and inspected at least monthly or more depending on its usage and governing industry standards if it is a sanitary process. During the cleaning procedure removable impellers or mixer shaft should be inspected for excessive wear, corrosion, and cracks—particularly at weld joints. Set screws and gib keys, if applicable, should be checked for proper thread fit and assembly. This is also a great opportunity to inspect the interior and exterior of your mixing tank, mixer stand and other mechanical system components to ensure that all are in proper shape and working to their full ability. This process can seem time consuming, but the time spent will translate to money saved in the long run.
Gearbox Lubrication
If the mixer is a gear-driven model, the gearbox is key to the life of your mixer. Listen for unusual noise and check for excessive heat generation. Consult your mixer manual and that of the gearbox, itself, to determine if additional gearbox lubrication is needed. The manual specifies what type of lubricant is required. Also, pay particular attention if operating in an FDA food grade or higher aseptic application. If not maintained regularly, high friction will lead to premature gearbox failure.
Motor and Mechanical Seals
Electric motors are generally low maintenance and require little direct intervention. However, increasing noise from an electric motor can indicate a motor bearing problem. It should be rare on newer mixers but a defective bearing can occur. Noise from the motor on an older mixer can be indicative of the need for a mixer motor replacement. Pneumatic motors also require periodic inspection and maintenance. The most common cause of premature air motor failures is dirty air supply lines, moisture in the lines, and failure to provide lubrication. A filter-regulator-lubricator (FRL) should be installed in the plumbing just upstream of the mixer for maximum motor life. For older air motors, rebuild kits are available. Finally, if the mixer was supplied with a mechanical seal, it should be inspected for wear of the sealing surfaces. Increased noise from seals can also be an indicator that the seal should be rebuilt or replaced. Depending upon the seal type rebuild kits may be available.
Use the Mixer for Its Intended Purpose
While industrial mixers are often used to process multiple batch types to save from buying multiple pieces of equipment, most were designed and built for specific application. A common cause of premature mixer failure is using it for multiple purposes including those that are beyond its design limits. When buying mixers to use for multiple operations, always provide your INDCO customer service representative or engineer with the properties of the most demanding application—that can be due to high density (weight per gallon), viscosity, or simply the need for very aggressive agitation. It’s recommended that, whenever possible, operators should add materials to a mixing vessel moving from lower viscosity to higher viscosity liquids. For formulations where this is not possible consult with a mixer engineer to assure the mixer is designed for the mechanical load.
Don’t Wait to Replace Parts
A heavy duty mixer is only as powerful as the sum of its parts. At INDCO, our mixer equipment is constructed with high quality materials optimized for trouble-free operation, so the need for service or parts should be minimal if the above steps are followed. However, mixers subjected to high stress and wear over time will eventually need to be addressed, and to keep your mixer working at top capacity, you shouldn’t wait to make repairs that can become even more expensive if they are put off.
How is your industrial mixer doing? If your equipment needs repairs, INDCO offers a variety of replacement parts including motors (air or electric), gearboxes, mounting brackets, clamps, bearings, and shafts to keep your mixer in top shape. If you think it might be time for an upgrade, you can view our commercial mixing machines online or in our digital catalog at any time. Our customer service team is always available to answer any questions, or, if you are ready to discuss customized solutions with an expert INDCO engineer, visit our contact page today or call us at 1-800-851-1049 to get started.