Stainless Steel Mixing Tanks 101: Open-Top Mixing Tanks
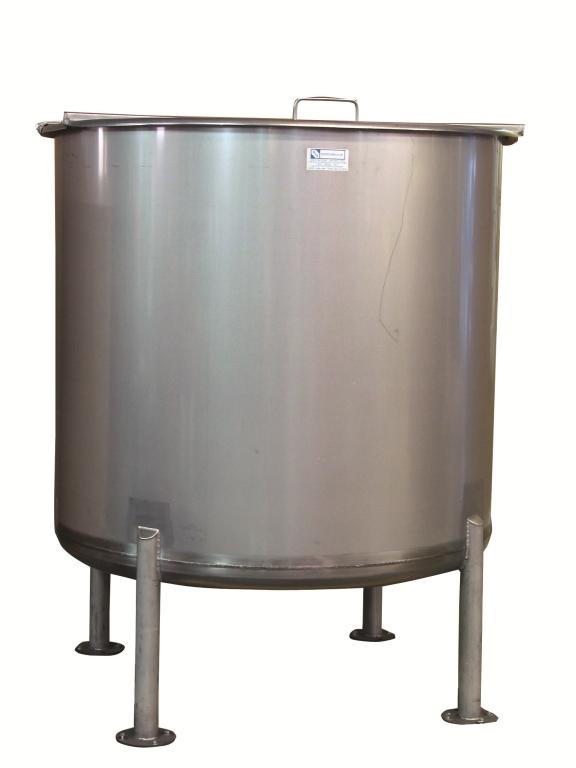
Producers of liquid products have used industrial mixing tanks fabricated from stainless steel alloys for many years. Common variations of open-top mixing tanks include simple open tanks used to mix paints and chemicals, deluxe finish sanitary tanks well suited for use in food processing and cosmetics production, and completely sealed aseptic containers vital to the pharmaceutical and biotech industries. With a vast array of applications for open-top mixing tanks, there is an equally diverse number of questions from our customers. Our goal at INDCO is to give you the knowledge to make an informed decision about the products your industry needs, and today, we are here to take a deeper dive into the topic of open-top mixing tanks in this first of two blog posts dedicated to stainless steel mixing tanks.
This post provides an overview of industrial grade steel mixing tanks and the different shapes these tanks offer. Looking for more information about sealed aseptic mixing tanks and vessels? Check out our Stainless Steel Mixing Tanks 102!
Getting Started: Open-Top Stainless Steel Mixing Tank Benefits
A quality product begins with quality equipment. The material utilized in the construction of a proper industrial mixing tank has a purpose. Stainless steel is not merely for aesthetic purposes—it is vital to producing a uniform product that meets the rigorous standards of industry use. Stainless steel industrial mixing tanks provide the benefit of a smooth, non-reactive and easy-to-clean surface. Stainless steel tanks are highly versatile, making them a solid investment for a variety of mixing needs including both liquid to liquid and liquid to solid mixing applications. These tanks, constructed of 304 or 316 stainless steel, also boast corrosion resistance across a wide range of chemicals from alkaline too acidic.
The designation as an “industrial grade” tank refers to a simply-constructed, single wall vessel utilized at atmospheric pressure. These tanks are most often used for open top mixing using a portable mixer and are available with standard mill 2B or optional deluxe polished finish. A loose-fitting lid is often ordered to prevent splashing or to protect the contents from contaminants. A hinge in the lid can be provided to allow access for viewing or addition of ingredients. The tank wall and bottom head are usually 10- to 14-gauge material.
Whether you are mixing industrial products such as adhesives or producing more sanitary products such as dairy other food products, a properly designed open top tank can be your solution.
A Closer Look at the Construction of an Open-Top Stainless Steel Mixing Tank
Consisting of 18% chromium and 8% nickel, 304 stainless steel is the most widely used stainless steel alloy for general industrial mixing tanks and for food production. It provides resistance to rust and corrosion and is easy to clean. When increased corrosion resistance is a necessity, 316 stainless steel can be specified as an option with marginally higher cost. It contains 2% molybdenum in addition to the chromium and nickel which significantly improves its chemical resistance to chlorides, bromides, fatty acids, and sulfuric acid.
Our industrial tanks have a 2B mill satin finish and welds are ground and brushed. All of our tanks can be ordered with a deluxe polished finish, which is a #4 finish, with welds ground smooth and polished suitable for food production or for when a smoother finish is required to promote cleaning. See our surface finish guide for more detail.
What Shape of Stainless Steel Mixing Tank is Right for Me?
The geometry of your industrial mixing tank can have just as much of an impact as the material selection. Common industrial mixing tank bottom configurations are conical, elliptical, and sloped—each of which are best suited for different states of matter, composition, and viscosities.
1. Conical: The conical design is best for the most complete drainage to a center located drain. This configuration is popular for liquids that blend easily with other liquids or powders, with little risk of unmixed materials gathering beyond the reach of the mixing impeller.
2. Elliptical: A dished bottom is best when it is important for the impeller to effectively suspend settled materials, and provide maximum batch turnover before draining.
3. Sloped: Finally, the sloped bottom design directs the liquid flow to a horizontally mounted drain valve or spigot at the bottom of the tank wall.
A formed lip around the perimeter of the top of the tank, pipe legs with mounting flanges and mixer mounting brackets are also common features for open top industrial tanks regardless of bottom configuration.
Finding the Right Open-Top Stainless Steel Mixing Tank
At INDCO, our goal is to help you optimize your industrial mixing processes and workflow. Our team of experienced customer service representatives and mixer applications engineers are here to help you find the perfect open-top or stainless steel mixing tank for your industry’s needs. Contact us to get in touch with us today! You can also submit the requirements for your industrial mixing tank by completing the INDCO tank data worksheet, or by contacting us. We are always happy to design customized solutions with specific material properties, batch size, and type of mixing process in mind.