8 Common Misconceptions about Industrial Mixing
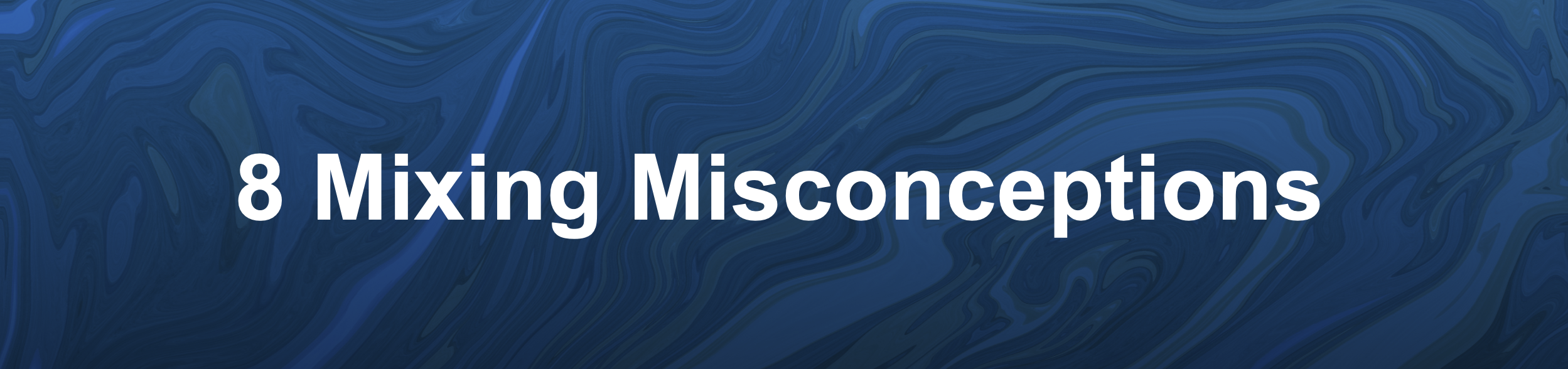
In the dynamic world of industrial mixing, the gap between fact and fiction can be as wide as the variety of mixers available in the market. As professionals in the industry, we at INDCO are here to dispel some common misconceptions that can lead to suboptimal choices and hinder the efficiency of your operations.
Misconception 1: One Mixer Fits All Applications
The idea that a single mixer can meet the requirements of all mixing applications is akin to believing a single key can open every lock. Each mixing application has unique characteristics – viscosity, particle size, mixing time, and shear sensitivity, to name a few. Selecting the right mixer, be it a high-shear mixer for emulsions or a lab mixer for precision, is crucial for achieving the desired outcome. Understanding the specific needs of your application is the first step towards making an informed decision. At INDCO, our applications engineers are ready to answer any question you may have about mixing and set you up with the perfect tools for your specific application.
Misconception 2: Mixing Time is Always Proportional to Batch Size
A common myth is that the time required for mixing is directly proportional to the size of the batch – larger batches need more time, and smaller ones need less. However, this isn’t always true. The mixing time depends on the mixer type, the materials being mixed, and the desired process outcome. Using an undersized mixer in a scaled-up application can result in long mix times. However, a properly scaled mixing system results in better operational efficiency, i.e. shorter mix times. Understanding the capabilities of your mixer with consideration of the batch size and material properties is critical.
Misconception 3: The More Aggressive the Mixing, the Better the Result
There's a belief that more aggressive mixing yields better results. This is not necessarily true, as over-mixing can lead to issues such as air entrapment, heat generation, or even breakdown of the materials. Gentle mixing might be required for sensitive materials to maintain their integrity. The key is to balance the intensity and duration of mixing to achieve the desired outcome without compromising the quality of the batch.
Misconception 4: Manual Mixing is a Viable Alternative for Small Batches 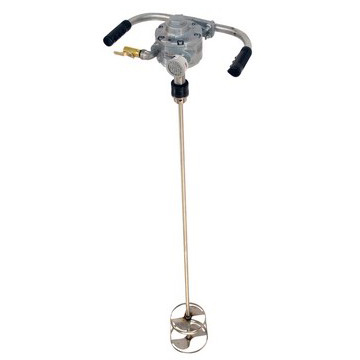
While manual mixing might seem adequate for small batches, it often lacks consistency and efficiency compared to mechanical mixing. Even for small-scale operations, a suitable industrial mixer like our handheld mixers or drill attachments can ensure uniformity, save time, and reduce labor costs. The investment in a small-scale mixer can significantly improve the quality and consistency of the product.
Misconception 5: All Mixers Require the Same Maintenance Routine
Maintenance routines can vary significantly depending on the type of mixer, relevant industry operational and sanitization protocols and usage. Assuming that all mixers are maintained using the same checklist, or worse, not maintained at all can lead to premature wear, affecting the mixer's performance and lifespan. It's important to follow the manufacturer's guidelines and tailor the maintenance plan to the specific needs of your equipment.
Misconception 6: Regularly Running a Mixer at Maximum Speed Wears Down the Machine and Reduces Its Longevity 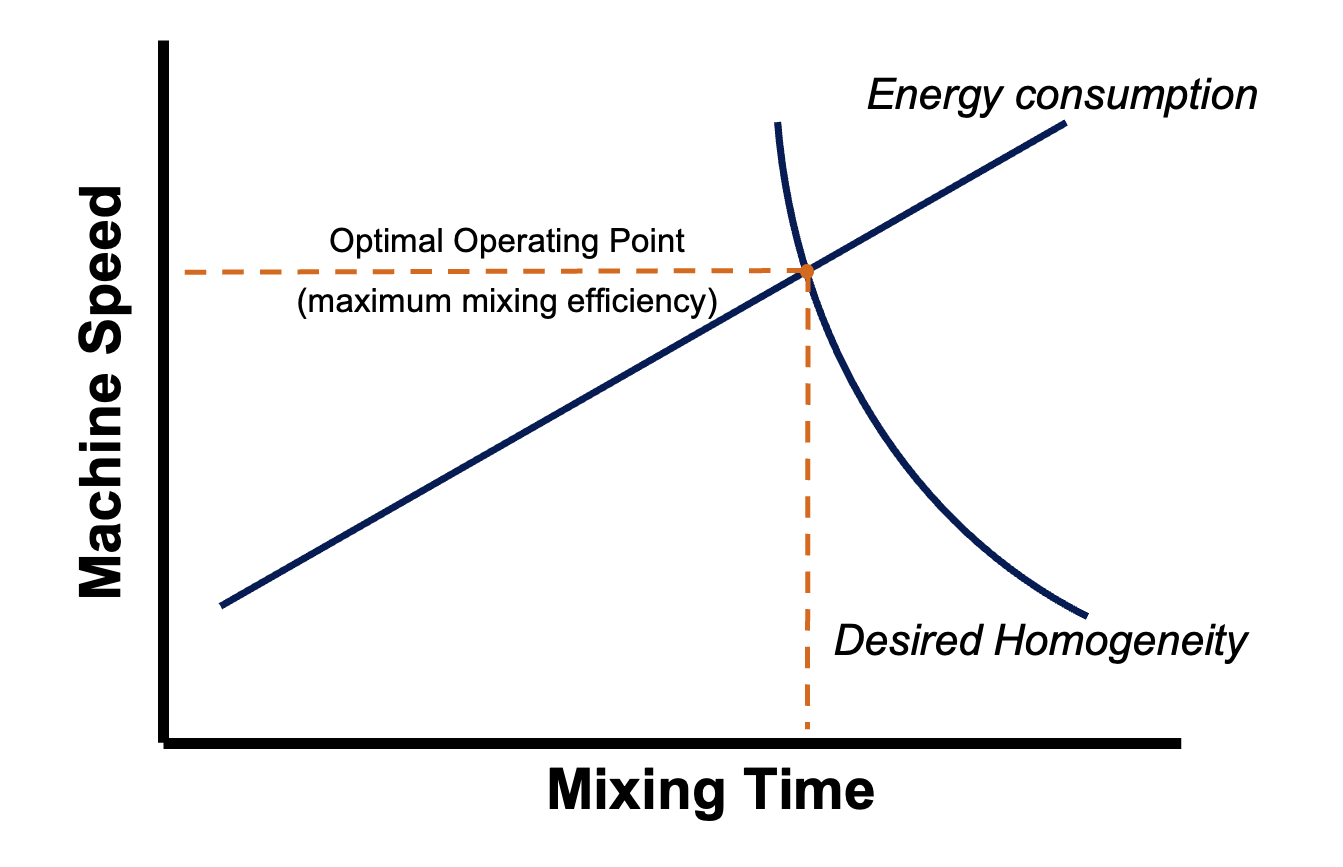
This misconception stems from a partial truth. While constantly operating at maximum speed can accelerate wear of moving components, modern mixers are designed to withstand high-speed operations especially if operated within the mixer’s specified operating range. It’s also important to consider viscosity, density, volume and other relevant factors in the mixing process. These factors will be crucial in determining your optimal mixing process (optimal operating point) where the highest possible efficiency is achieved. When all of this is considered, it’s possible that the optimal operating speed may actually be the maximum speed of your mixer. This tends to be especially true for very low viscosity applications.
Misconception 7: A Larger Motor Means Better Results
While it's beneficial to not be horsepower limited, more power is not always the answer for the best mixing system. The effectiveness of a mixer is not solely dependent on the motor's rating but on how well it's matched to the mixer's design and the application's requirements. A larger motor does not guarantee better mixing and a significantly oversized motor can lead to unnecessarily high energy consumption and therefore higher costs. The focus should be on finding a mixer with the right motor specifications that align with your available utilities and mixing needs.
Misconception 8: Only Large Companies Can Afford Quality Industrial Mixing Machines
This is a myth that discourages many small to medium-sized enterprises from investing in quality equipment. The truth is, the market offers a wide range of mixing solutions suitable for different budget scales. Additionally, investing in a high-quality mixer can be cost-effective in the long run due to its efficiency, durability, and lower maintenance costs. Quality doesn't always mean unaffordable; it's about finding the right balance between price and performance.
Conclusion
In conclusion, navigating the complex landscape of industrial mixing requires a nuanced understanding of equipment and processes. By debunking these common misconceptions, we hope to guide you towards making informed decisions that optimize your mixing operations. Remember, the key to successful industrial mixing is not just in the equipment, but in the knowledge of how to use it effectively.
Check out our article “INDCO Industrial Mixing Design 101: A Basic System Design Guide” to learn more about the industrial mixing process and get insights into how INDCO designs quality mixers. Our engineers may also be contacted directly to ensure an in depth understanding of your specific applications. Contact us online or call us at 1-800-851-1049.