What is a sealed mixing system?
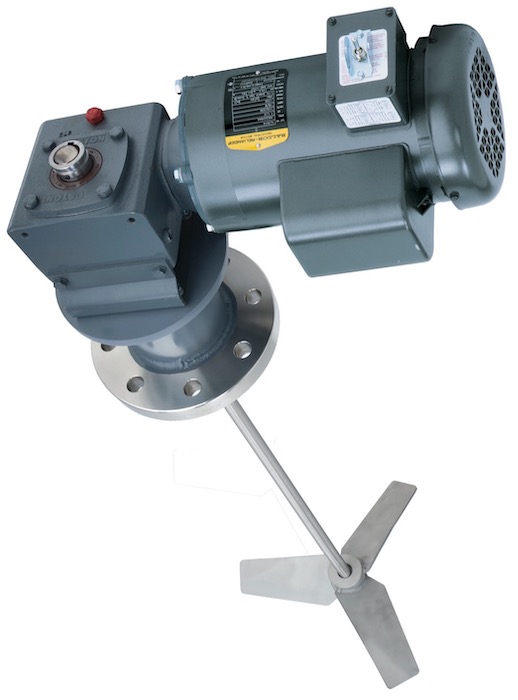
Industrial mixing systems comprised of a mixing tank and a mounted rotating shaft mixer are extremely commonplace in liquid batch production and continuous process applications. Most systems are open top or perhaps covered with a mixer that is top-mounted, side-mounted or bottom-mounted. These set-ups are simple and economical as long as the process can be successfully completed without pressure, there are no hazards from the batch contents or a sterile environment is not a must. For a relatively small percentage of mixing applications, however, one or more of these situations applies.
Sealed mixing systems are configured to a number of different degrees and for a wide variety of reasons. Simple, low pressure mixing processes requiring control of fumes may be addressed with an elastomer lip seal, a single-piece round component with a center hole sized to run tightly against the rotating mixer shaft. Available in a wide range of materials, these seals are relatively inexpensive. Material selection is based upon the shaft speed and its compatibility with batch properties. Lip seals are only recommended for pressures of 5 psi or lower. More demanding sealed mixing systems are common in food, personal care and pharmaceutical industries where batch sterilization from contaminants is key or in cases where safety from hazardous contents is important. Sealed systems can also be necessary where heat and pressure serve as a catalyst for a chemical reaction to occur in the mixed batch.
System designs to address the needs of more complex processes are more expensive and often must meet defined industry-driven or regulatory specifications. Examples include the 3A dairy industry specification, ASME Bioprocessing Equipment specification for pharmaceutical and biotech industries and the ASME Boiler and Pressure Vessel Code for pressurized tanks. Mixers designed for high end sealed applications often feature mechanical seals. These two-piece components consist of rotating and stationary parts. The rotating component is set-screwed to the rotating shaft and has an o-ring seal to prevent gas leakage between it and the shaft. The stationary component is mounted in a housing with a gasket seal and the shaft passes through a center bore. Each half has an extremely smooth and hard surface, usually carbon or carbon compound, and the two surfaces run in direct contact during mixer operation. The highly polished surfaces allow rotation while limiting leakage to exceedingly small volumes.
INDCO offers mixers and tanks for sealed and sanitary sealed systems. For non-sanitary industrial mixing tank applications requiring a seal the FM-series and FMG-series ANSI flange mounted mixers can be configured with either a lip seal or a mechanical seal.
The PhG-series Tri-Clamp® mount mixer is built for the most stringent sanitary mixing applications up to 10,000 liters or 2,500 gallons. It features a hygienic mechanical seal mounted outside the tank just above the mounting surface. Designed for the pharmaceutical, food and cosmetics industries, the direct drive models are suited to lower viscosities of up to approximately 500 cps and the gear-driven models often apply to higher viscosities. However, gear-driven models are also commonly used for lower viscosities in order to minimize shear. The external dry-running mechanical seals are rated full vacuum to 200 psi and feature EPDM USP Class VI elastomer o-rings. Injectables and ophthalmic solutions are examples of products produced using Ph-series mixers.
INDCO's TCM-series Tri-Clamp® mount mixers are a more economical option that is also designed for sealed applications. The key difference is that a smaller mechanical seal is located on the underside of the mount and is, therefore, located inside the vessel. The internally-mounted mechanical seal is rated full vacuum to 125 psi. Personal care products such as lotions and fragrances are examples of products commonly produced using TCM mixers.
Sanitary sealed mixing tanks consist of heavier gauge construction than the open top industrial varieties. Heavy gauge elliptical heads normally comprise the tank lid and bottom. Lids are usually hinged with a gasket and hold-down clamps for smaller tanks whereas large vessels consist of a welded top head with access provided by ANSI flange manways. ASME Pressure Vessel and Boiler code design requirements must be met for applications exceeding 15 psi. The most common material of construction is 316 or 316L Stainless Steel. Molybdenum content of 2%-3% is what differentiates the 316 alloys from 304 and provides superior resistance to chemicals and corrosion. Highly polished and electropolished wetted surfaces, large radii and strict standards for weld and surface defects provide the sanitary and easily cleaned environment for the production of medical compounds and injectable drugs.
INDCO’s engineers are available to help you select the correct mixer for your application and we can also customize the system to meet your specific needs. Email our team at sales@indco.com for immediate assistance.