Difference between impellers and propellers in mixing
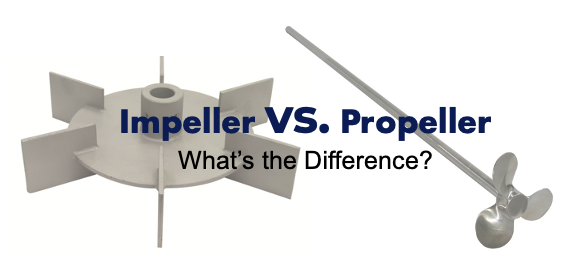
Propeller vs. Impeller
Technically speaking, propellers are a subset of impellers. This relationship is similar to a passenger car as a type of vehicle which can include sedans, SUV’s, vans, etc. all being referred to simply as “cars”. Industrial mixer customers often use the terms interchangeably or frequently refer to the mixing “propeller” generically to represent any of the possible impeller types that may be on a mixer shaft. The marine style mixing propeller is named based on its visual likeness to the common boat propeller design. This familiar geometry provides efficient flow with relatively low shear stress imparted to the mixture or batch. It is a common choice for higher speed mixing operations focused on blending low viscosity miscible liquids or liquids and solids that dissolve readily and can be used successfully at either low or high speed. The most common variations of the marine style propeller include the three-blade square pitch and the steep pitched designs.
Types of Mixing Impellers
In the context of mixing, impellers are categorized primarily based on the flow patterns they generate, as well as their specific use cases. Two main categories are axial flow impellers and radial flow impellers. Axial flow impellers produce fluid motion that runs parallell to the mixing shaft and, as one might expect, radial flow designs produce flow that moves primarily outward from the mixing shaft. Examples of each type are axial flow turbines and radial flow turbines. These impeller types feature broad, flat blades required for mixing higher viscosities. They are less efficient than the marine style and produce greater shear forces but have the higher surface contact necessary for heavier mixtures.
Another example of a radial flow impeller is the Rushton turbine, which features a disk with multiple flat blades mounted perpendicular to the axis of rotation. It is commonly used in fermentation and other sparging applications where gases are introduced into an aggressively agitated vessel.
It's worth noting that there are many specialty impeller designs such as mixed flow impellers, which generates a unique gentle flow that is partly axial and partly radial. This provides a balance between the flow characteristics of axial and radial propellers, making it a versatile option for a wide range of lower viscosity mixing.
Ultimately, the choice of mixing impeller design depends heavily on the nature of the mixing process, the characteristics of the fluids involved, and the desired end product.
Stainless Steel vs Aluminum Marine Style Propellers
Industrial mixer manufacturers normally offer 316 stainless steel as the standard materials for parts to be submerged in a mixing application. Numerous advantages come with the application of stainless steel in mixing environments including chemical resistance as well as protection against rust and corrosion. Nearly every mixer featured on the INDCO website and catalog showcases stainless steel across all parts that are in direct contact with fluids. However, for those most demanding chemical or corrosive environments some alternative materials such as Hastelloy are available.
If chemical resistance is not an issue, propellers constructed of aluminum can be a very economical cost saving option. INDCO offers an aluminum option for marine style impellers. From the 3” diameter left hand model up to the 15” model, cost savings can range from approximately $35 per propeller to as much as $500 each.