All-Stainless or Epoxy Coated: The Pharma Mixer Choice and Price
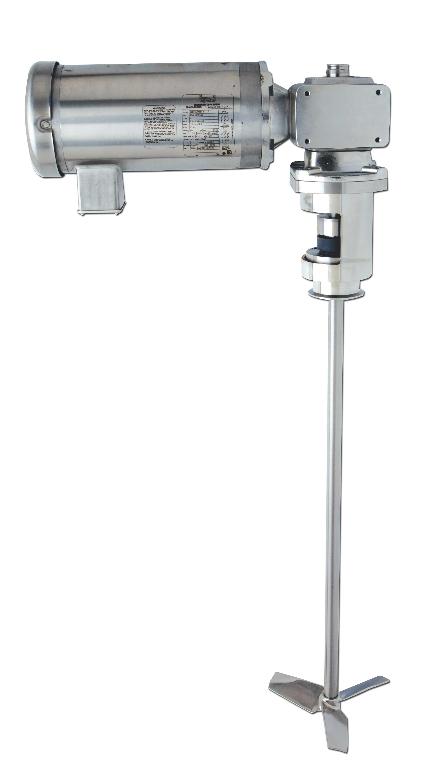
Mixer manufacturers produce sanitary mixers for the pharmaceutical and biotech industries using a variety of materials including all-stainless steel and epoxy coated. Although the wetted shaft and impellers are usually at least 316 stainless steel, the materials used for motor mounts, mechanical seal housings, gear reducers and motors are not nearly as uniform. Industry governing specifications favor uncoated high grade alloys for all materials of construction in order to stand up to cleaning solutions and processes. Epoxy-coated washdown components are often acceptable alternatives to stainless steel. However, all coatings wear and potentially flake over time producing a possible source of batch contamination.
The tradeoff of selecting coated or aluminum components versus a design utilizing all stainless steel is equipment cost. Manufacturers generally offer a given mixer model at different price points dependent upon the component materials selected. Stainless steel components are significantly more expensive than coated versions. This is due to the higher cost of raw stainless steel, the relatively higher cost of processing it and the much lower production volumes versus standard industrial grade components.
As an example, let’s review the INDCO PHG-100T3. This ”high end” one-horsepower all-stainless steel gear-driven mixer with a single mechanical seal sells for about $13,000. It features polished 316 stainless steel wetted parts as expected for this type of mixer. Additionally, the electric motor, gear reducer and all motor mounting and seal housing parts are 316 stainless steel with no paints or coatings. Many applications do not offer the flexibility to use a less expensive mixer but for those that do INDCO offers this mixer with a washdown epoxy coated motor and gearbox. Substituting these components can reduce acquisition cost by up to 20% resulting in a $2,600 savings in this example.
Customers should carefully consider material selection relative to aseptic mixing requirements for each product or production environment. Call our INDCO applications engineers to optimize your equipment costs and process needs.