4 Preventive Maintenance Tips for Dispersers
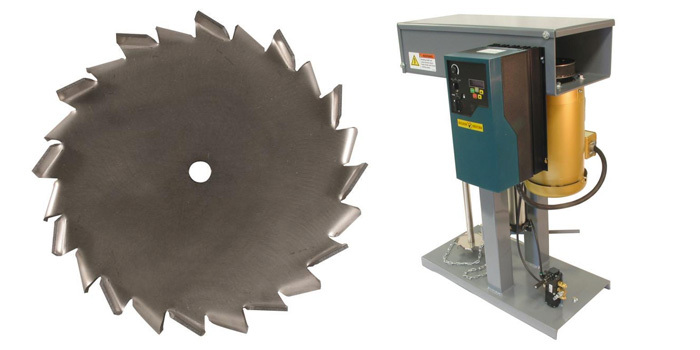
At INDCO, we offer a full line of dispersion equipment from fractional-horsepower benchtops to 20-horsepower floor-mounted models fit for any application. Our selection of high-shear dispersers includes a variety of air-powered or electric options that are suitable for a variety of industry uses — from pharmaceutical laboratories, food and beverage operations, chemical production, paint pigment dispersion, construction and more.
Our dispersers are built for reliability and longevity, but to maintain a healthy lifespan for your product, it’s important to understand how they work, and what can be done to keep them working optimally.
HOW DISPERSERS WORK:
If you’re asking, “What is a disperser? How does it work?”, you’re in luck. Dispersion is a high-speed, high-shear process requiring more horsepower to achieve than simple agitation and blending. Often confused with “mixing,” dispersion goes past the mixing process of blending two or more individual ingredients through rotational flow and uses a shear-driven process to break down solid ingredient particles.
The dispersion process:
- The dispersion blade turns.
- Particles make contact with the blade within the vessel and are broken apart.
- Flow then divides into upward and downward components at the vessel wall, ensuring complete circulation.
- Beyond the zone of attrition (the area where the internal collisions occur), the broken-down material is thoroughly mixed, and the particles are dissolved or dispersed by the horizontal laminar flow extending from the blade.
HOW TO MAINTAIN YOUR DISPERSER.
To ensure the longevity of your high-shear disperser, there are a few basic preventive maintenance steps to keep it running smoothly. When properly maintained, dispersers can work for years without issue — making sure your output stays consistent.
Monitor blade tooth wear and replace when needed.
The disperser’s production of a homogeneous liquid product results from the high shear action of the blade. Dispersion blades consist of teeth that have an abrupt edge profile that naturally wears over time. The rate of wear varies and is dependent upon the batch contents. Abrasive solids such as silica sand greatly accelerate blade wear. As the blade edge becomes rounded and smooth versus the original squared off profile process results will begin to suffer. Therefore, frequent inspection of the blade and replacement when worn is critical to obtaining desired process outcome.
Maintain the motor.
Dispersers are driven at high speeds to reach the required blade tip speeds of 2500 to 5000 feet per minute associated with the dispersion process. Therefore, motor maintenance is very important. Most electric motors are relatively maintenance free. However, electric motor overload is the most common cause of premature failure. For each new application, particularly those of high viscosities or high solids content, monitor the motor temperature during qualification. Most electric motors include an overload circuit that will trip before burning the windings but motors that run continually near their temperature limits will have a shorter life.
Air-powered motors will not burn out but will simply stall if overloaded. To ensure optimal long-term performance the air supplied should be free of dirt water and condensation and the motor should be lubricated. See the air motor manual or speak to your INDCO engineer about filter-regulator-lubricator (FRL) systems to protect your air motor. Air motor rebuild kits are also available for use with an aging air motor and may be an option versus replacement.
Carefully watch the bearings and shaft vibration.
Equipment with rotational shafts are subject to critical speeds. Critical speeds are those at which a natural frequency of the machine exists and shaft vibration is amplified. Engineers design equipment such that critical speeds do not fall within the intended speed range over which the dispersers are normally used. It is common, however, to experience a critical speed while ramping up the shaft rpm to the desired operating speed. Damage to the shaft and bearing system can result from running long-term at a critical speed. To prevent this the rpm should be increased rapidly through a range where increased vibration is noted. Additionally, a disperser should never be run dry, i.e. without the blade submerged in liquid as doing so will increase the degree of vibration dramatically causing potential bending of the shaft and damage to bearings.
Maintain a routine cleaning schedule.
Over time, buildup of debris and ingredient remnants in and around your disperser can be problematic. Develop a cleaning schedule for the disperser’s blade, shaft and bearing housing. Clean any accumulating ingredients on the exterior of your machine including all electronic or pneumatic controls and peripheral equipment.
If you have any questions about dispersers or maintenance, INDCO provides unparalleled quality with unparalleled care. To talk to a customer service representative or work with one of our engineers, visit our contact page today or call us at 1-800-851-1049.