The Fundamentals of Dispersion in Mixing
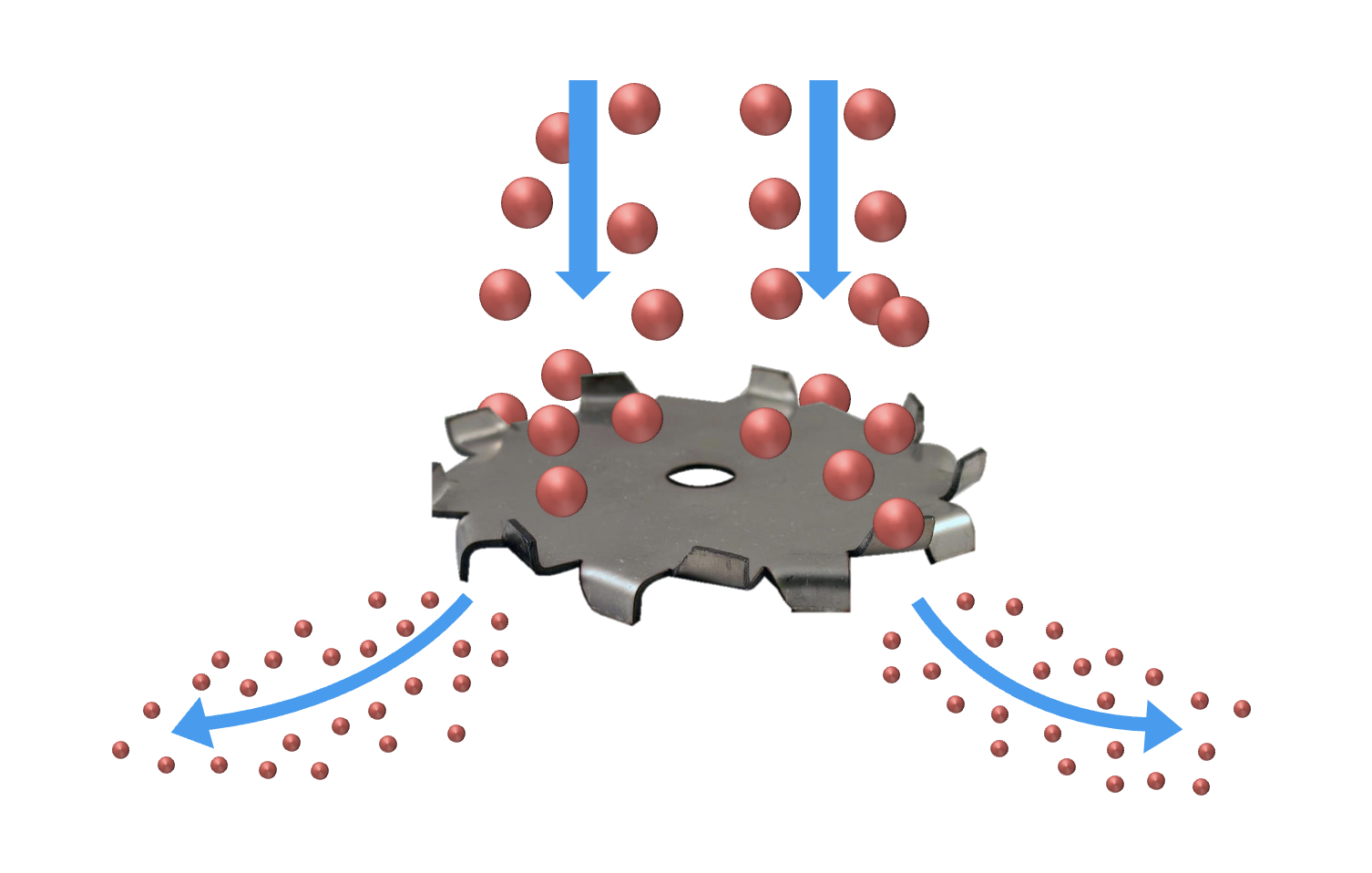
Fundamentals of Dispersion: A Quick Reference Guide
At INDCO, we specialize in manufacturing a variety of dispersion blades and disperser equipment. Understanding the key concepts surrounding dispersion is crucial before ordering your high-speed disperser blade or dispersion blade.What is a Dispersion Blade?
A dispersion blade is a key component in the process of dispersion. It is designed to break apart particles when it rotates at high speeds, facilitating the dispersion process. The blade size should measure about 1/3 the diameter of the vessel in which the blade will be used. The blade should be placed about one full blade diameter off the vessel bottom.How Does Dispersion Work?
Dispersion is a high-speed, high-shear process that requires more horsepower to successfully achieve than simple agitation. As the dispersion blade turns, particles contact the blade and are broken apart. In the intense turbulence surrounding the blade, particles collide at high speeds and are further broken apart.Beyond the zone of attrition (the area directly adjacent to the blade trailing edges), the now broken-down material is thoroughly mixed, and particles are dissolved or dispersed by the horizontal laminar flow extending from the blade. The flow then divides into upward and downward components at the vessel wall, ensuring complete circulation.
For a more in-depth explanation, check out our blog “How Dispersion Works” .
How to Get the Most from Your Dispersion
To get the best results from your dispersion process, you need to determine the optimum blade size, blade position, and material depth for your project. The maximum depth of the material should not exceed three times the diameter of the blade. The depth above the blade should not be less than the amount below the blade. Round vessels always provide better dispersion than square vessels because they have no “dead areas” in the corners.
Choose the correct blade
When choosing your blade design, know that all INDCO blade designs produce high shear as their primary function. INDCO’s design A, B, C, and D blades will vary more in their pumping action than their shearing ability. A dispersion blade’s pumping capacity refers to how effectively it can move material around the vessel. Good pumping action is related to the size and shape of the blade's teeth. A good way to think of it is comparing it to a box fan. If a fan has larger blades and/or blades sloped more aggressively, the amount of wind it creates will be greater. In this case, the fan blades are similar to the teeth around the edge of a dispersion blade. INDCO’s Design A and E blades have the lowest pumping ability due to their smaller teeth size. Compared to Design B, Design C, and Design D which provide increasingly higher pumping capacity. Design D blades specifically features two different styles of aggressively sloped blade teeth in order to increase pumping capacity.View infographic on how to choose a dispersion blade
How to Calculate Tip Speed
Shear is largely determined by the tip speed (or rim velocity) of the blade. The faster the tip speed, the higher the shear. Tip speed should generally be from 4,000-6,000 feet per minute. The diameter of the blade will determine the RPM the shaft must turn to give the recommended tip speed. To calculate tip speed in feet per minute, multiply shaft RPM x 0.262 x blade diameter in inches.
EX: 3000 x 0.262 x 6 = 4716
If you have more questions or need help choosing the parts for your system, we are always here to help.
Contact the INDCO team